Project
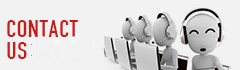
Contact person: Zhang Xingqian 13912340688
phones: 0519-81182602
Fax: 0519-81182602
whatsapp:+8618961131360
Website: www.qinmianbs.com
Email: yz@qinmianbs.com steven@qinmianbs.com
Lithium carbide disc dryer
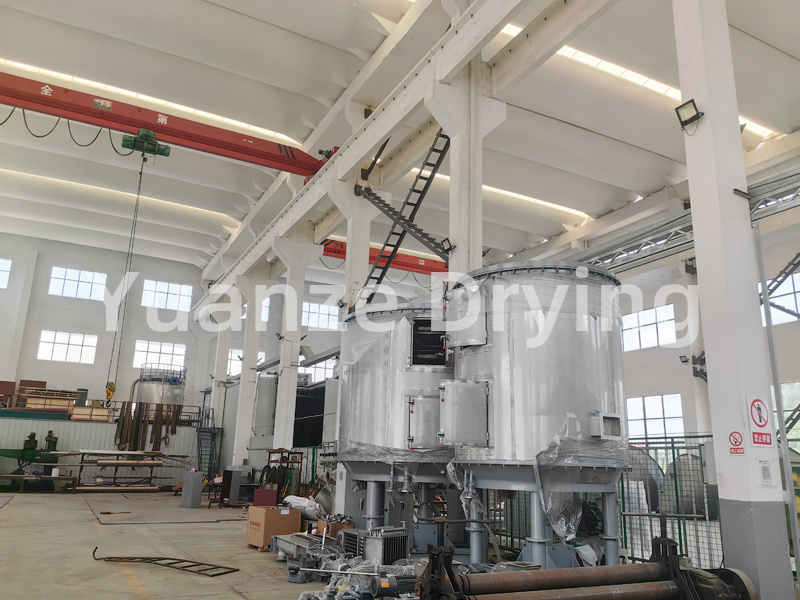


Lithium carbide disc dryer
Description
A disc continuous dryer is a conductive continuous drying equipment. Its structure and working principle determine its high thermal efficiency, low energy consumption, small footprint, simple configuration, convenient operation and control, and good operating environment. It is widely used in drying operations in industries such as chemical, pharmaceutical, pesticide, food, feed, and agricultural by-product processing. Highly praised in practical use in various industries. We currently produce and manufacture three types: atmospheric pressure, sealed, and vacuum, with four types: 1200, 1500, 2200, and 3000. A (carbon steel), B (stainless steel is uniformly distributed in the contact material), and C (on the basis of B, stainless steel is added to the steam pipeline, main shaft, and support, and stainless steel is lined on the cylinder and cover). A series of products with three types of materials and a drying area of 4-180m2, totaling hundreds of models, and can provide matching auxiliary equipment to meet the needs of users for drying various materials.
Wet materials are continuously added from the feeder to the upper layer drying plate of the dryer, and the rake arm with rake blades rotates to continuously flip the materials. The material flows through the surface of the drying tray along an exponential spiral. The material on the small drying tray is transferred to the outer edge and falls to the outer edge of the large drying tray below. On the large drying tray, the material moves inward and falls into the next layer of small drying tray from the middle discharge port. The large and small drying plates are arranged alternately up and down, allowing materials to continuously flow through the entire dryer. The hollow drying plate is filled with heating medium, which includes saturated steam, hot water, and thermal oil. The heating medium enters from one end of the drying plate and exits from the other end. The dried material falls from the last layer of the drying plate to the bottom layer of the shell, and is then transported by the rake blades to the discharge port for discharge. Moisture escapes from the material and is discharged through the dehumidification port located on the top cover. The moisture in the vacuum disc dryer is discharged through the vacuum pump port located on the top cover. The dry materials discharged from the bottom layer can be directly packaged. By adding auxiliary machines such as finned heaters, solvent recovery condensers, bag filters, dry material mixing mechanisms, and induced draft fans, the drying production capacity can be improved. Drying paste like and heat sensitive materials can easily recover solvents and perform pyrolysis and reaction operations.
(1) Easy regulation and strong applicability
By adjusting the thickness of the material layer, spindle speed, number of rake arms, rake blade type and size, the drying process can be optimized.
Each layer of drying tray can be separately heated or cooled by adding hot or cold media to the material, and the temperature control of the material is accurate and easy.
The residence time of materials can be precisely adjusted.
The material has a single flow direction, no backmixing phenomenon, uniform drying, stable quality, and no need for further mixing.
(2) Easy to operate and operate
The operation of driving and stopping the dryer is very simple.
After stopping the feeding, the material scraper can quickly empty the material inside the dryer.
Through the special large inspection door mirror, the inside of the equipment can be cleaned and observed very carefully.
(3) Low energy consumption
The material layer is very thin, the spindle speed is low, and the power required for the material conveying system is small, resulting in low power consumption.
Drying through heat conduction has high thermal efficiency and low energy consumption.
(4) Good operating environment, recyclable solvents, and dust emissions meet requirements
◎ Atmospheric type: Due to the low airflow velocity inside the equipment and the low humidity distribution in the equipment, it is difficult for dust to float to the top of the equipment. Therefore, the exhaust gas discharged from the top dehumidification outlet contains almost no dust.
Sealed type: equipped with a solvent recovery device, it can conveniently recover organic solvents from moisture carrying gases. The solvent recovery device is simple and has a high recovery rate. For flammable, explosive, toxic, and oxidizable materials, nitrogen can be used as a moisture carrying gas for closed-loop circulation, ensuring safe operation. Especially suitable for drying flammable, explosive, and toxic materials.
Vacuum type: a disc dryer operated under vacuum, especially suitable for drying thermosensitive materials.
(5) Easy installation and small footprint
The dryer is manufactured as a whole and transported as a whole. It only needs to be lifted and positioned, making installation and positioning very easy.
Due to the layered arrangement and vertical installation of the drying tray, even with a large drying area, the occupied area is also very small.
specifications | outside diameter mm | height mm | drying area m2 | power Kw |
1200/4 | Φ1850 | 2718 | 3.3 | 1 |
1200/6 | 3138 | 4.9 | ||
1200/8 | 3558 | 6.6 | 1.5 | |
1200/10 | 3978 | 8.2 | ||
1200/12 | 4398 | 9.9 | 2.2 | |
1500/6 | Φ2100 | 3022 | 8.0 | |
1500/8 | 3442 | 10.7 | ||
1500/10 | 3862 | 13.4 | ||
1500/12 | 4282 | 16.1 | 3.0 | |
1500/14 | 4702 | 18.8 | ||
1500/16 | 5122 | 21.5 | ||
2200/6 | Φ2900 | 3319 | 18.5 | |
2200/8 | 3739 | 24.6 | ||
2200/10 | 4159 | 30.8 | 4.0 | |
2200/12 | 4579 | 36.9 | ||
2200/14 | 4999 | 43.1 | 5.5 | |
2200/16 | 5419 | 19.3 | ||
2200/18 | 5839 | 55.4 | 7.5 | |
2200/20 | 6259 | 61.6 | ||
2200/22 | 6679 | 67.7 | 11 | |
2200/24 | 7099 | 73.9 | ||
2200/26 | 7519 | 80.0 |
specifications | outside diameter mm | height mm | drying area m2 | power Kw |
2500/6 | Φ3150 | 3319 | 26.3 | 4 |
2500/8 | 3739 | 35 | ||
2500/10 | 4159 | 43.8 | 5.5 | |
2500/12 | 4579 | 52.5 | ||
2500/14 | 4999 | 61.3 | 7.5 | |
2500/16 | 5419 | 70 | ||
2500/18 | 5839 | 78.8 | 11 | |
2500/20 | 6259 | 87.5 | ||
2500/22 | 6679 | 96.3 | ||
2500/24 | 7099 | 105 | 13 | |
2500/26 | 7519 | 113.8 | ||
3000/8 | Φ3800 | 4050 | 48 | 11 |
3000/10 | 4650 | 60 | ||
3000/12 | 5250 | 72 | ||
3000/14 | 5850 | 84 | ||
3000/16 | 6450 | 96 | ||
3000/18 | 7050 | 108 | 13 | |
3000/20 | 7650 | 120 | ||
3000/22 | 8250 | 132 | ||
3000/24 | 8850 | 144 | ||
3000/26 | 9450 | 156 | 15 | |
3000/28 | 10050 | 168 |